जैसा कि हम सभी जानते हैं, निवेश कास्टिंग का उत्पादन होता हैकास्टिंग्ससटीक परिशुद्धता और अच्छी फिनिश के साथ। हालाँकि, उत्पादन प्रक्रिया के दौरानधातु - स्वरूपण तकनीक, कई संभावित सामान्य कास्टिंग दोष हैं। अपने इंजीनियरिंग अनुभव और उन्नत उपकरणों के आधार पर, हम कारणों का विश्लेषण करके ऐसी समस्याओं को रोकने का एक तरीका ढूंढ सकते हैं। नीचे, हम कई सामान्य कास्टिंग दोषों और उनके कारणों और रोकथाम के तरीकों का परिचय देते हैं। आशा है कि यह लेख हमारे ग्राहकों की समस्याओं को समझने में सहायक होगा और हमारे सहकर्मियों के लिए, यह विश्लेषण संभावित कास्टिंग दोषों को रोकने में आपकी मदद कर सकता है।
अंडरकास्ट और ठंडा अवरोधक
1. समस्या विवरण:
अंडरकास्टिंग में अक्सर कास्टिंग की पतली दीवार में या आंतरिक धावक से दूर स्थानीय स्तर पर मांस की कमी होती है, और इसका किनारा चाप के आकार का होता है। ठंडा विभाजन यह है कि पिघली हुई धातु की दो किस्में पूरी तरह से जुड़ी नहीं हैं और स्पष्ट जोड़ हैं।
2. कारण:
1) कम पिघली हुई धातु डालने का तापमान और मोल्ड तापमान
2) डालने की गति धीमी है या रनर सेटिंग अनुचित है, धातु का प्रवाह बहुत लंबा है
3) ढलाई की दीवार की मोटाई बहुत पतली है, और पिघली हुई धातु का प्रवाह खराब है
4)डालते समय काट देना
3. निवारक उपाय:
1) पिघली हुई धातु डालने का तापमान और मोल्ड तापमान बढ़ाएँ
2) पिघली हुई धातु के प्रवाह को कम करने के लिए डालने की गति बढ़ाएँ या आंतरिक धावक की संख्या या क्षेत्र बढ़ाएँ
3) डालने के दौरान कट-ऑफ को रोकने के लिए पोरिंग राइजर के प्रेशर हेड को बढ़ाएं
संकुचन
1. समस्या का विवरण:
इसका पता केवल एक्स-रे निरीक्षण से ही लगाया जा सकता है। सतह का सिकुड़न प्रतिदीप्ति या धुंधला निरीक्षण द्वारा पाया जा सकता है। गंभीर मामलों में, इसका पता रेत उड़ाने के बाद लगाया जा सकता है।
2. कारण:
1) कास्टिंग संरचना अनुचित है, और हॉट स्पॉट बहुत अधिक या बहुत बड़े हैं
2) डालने वाले राइजर की ताप क्षमता छोटी है, जो अनुक्रमिक जमने में विफल रहती है, या दबाव सिर छोटा है, जिससे फीडिंग क्षमता कम हो जाती है
3) मोल्ड का तापमान कम है, शीतलन दर तेज है, और फीडिंग चैनल अवरुद्ध है
3. निवारक उपाय:
1) कास्टिंग संरचना में सुधार करें और हॉट स्पॉट को कम करें
2) राइजर को उचित रूप से सेट करें, या एक फीडिंग रिब जोड़ें जिसे प्रसंस्करण विधियों द्वारा हटाया जा सकता है, दबाव सिर बढ़ाएं, ताकिनिवेश कास्टिंगएक निश्चित दबाव सिर की कार्रवाई के तहत क्रमिक रूप से ठोस बनाया जा सकता है
3) शीतलन दर को धीमा करने के लिए डालने का तापमान और मोल्ड तापमान को उचित रूप से बढ़ाएं
गरम दरार
1. समस्या विवरण:
सतह पर या अंदर अनियमित अंतरकणीय दरारें उत्पन्न हो जाती हैं और सतह ऑक्सीकृत हो जाती है। इसे रेत की गंभीर सफाई के बाद देखा जा सकता है, और केवल हल्के प्रसंस्करण या प्रवेश निरीक्षण के बाद ही पाया जा सकता है।
2. कारण:
1) यह मिश्र धातु की संरचना से संबंधित है, कार्बन और सिलिकॉन की मात्रा अधिक है, तरल-ठोस चरण की तापमान सीमा बड़ी है, और गर्म क्रैकिंग आसान है
2) कम मोल्ड तापमान, खराब रिट्रीटबिलिटी और तेज़ शीतलन दर
3) कास्टिंग की मोटाई बहुत भिन्न होती है, और संक्रमण पट्टिका बहुत छोटी होती है
3. निवारक उपाय:
1) मिश्रधातुओं या स्टील्स के लिए जिनमें गर्म दरारें पड़ने का खतरा होता है, उनकी कार्बन और सिलिकॉन सामग्री को जहां तक संभव हो मध्य और निचली सीमा तक नियंत्रित किया जाना चाहिए।
2) डालने के दौरान मोल्ड का तापमान बढ़ाएं, कास्टिंग की शीतलन दर को धीमा करें, या मोल्ड शेल की ताकत कम करें
3) कास्टिंग की मोटाई के जोड़ों पर एंटी-क्रैकिंग प्रक्रिया पसलियों को जोड़ें, या संक्रमण फ़िललेट्स को बढ़ाएं
ठंडी दरार
नाम और विशेषताएँ:
ढलाई में लगातार दरारें पड़ रही हैं। फ्रैक्चर पर एक चमकदार सतह या थोड़ी ऑक्सीकृत सतह दिखाई देती है।
कारण
1. कास्टिंग की शीतलन प्रक्रिया के दौरान, सिकुड़न में बाधा आती है, जिसके परिणामस्वरूप थर्मल तनाव और चरण परिवर्तन तनाव होता है, और ये तनाव लोचदार अवस्था में सामग्री की ताकत से अधिक हो जाते हैं और फ्रैक्चर का कारण बनते हैं।
2. शेल की सफाई की प्रक्रिया में, गेट, राइजर को काटने या समायोजन के दौरान, अवशिष्ट तनाव के साथ कास्टिंग को फ्रैक्चर का कारण बनने के लिए बाहरी बल के अधीन किया जाता है।
रोकथाम के तरीके
1. आकृति की पीछे हटने की क्षमता में सुधार करने के लिए ठंडी दरारों पर कठोर पसलियाँ जोड़ें, जिससे सिकुड़न प्रतिरोध और कास्टिंग तनाव कम हो जाएगा।
2. कास्टिंग के बाद की प्रक्रिया में, कास्टिंग के बीच गंभीर प्रभाव से बचें।
छेद
नाम एवं विशेषताएँ
ढलाई पर चिकनी भीतरी सतह के साथ स्पष्ट या अगोचर छेद होते हैं।
कारण
1. मोल्ड शेल की खराब वायु पारगम्यता, जिससे डालने के दौरान गुहा में गैस को निकलने में बहुत देर हो जाती है।
2. शेल आकार की अपर्याप्त फायरिंग, जिसके परिणामस्वरूप शेल सामग्री में मोल्ड सामग्री के अवशेष और गैस उत्पादक सामग्री को अपर्याप्त रूप से हटाया जाता है।
3. धातु तरल गैस की मात्रा बहुत अधिक है, जिससे खराब डीऑक्सीडेशन होता है।
4. डालने वाली प्रणाली की सेटिंग अनुचित है, जिससे डालने में मानव गैस शामिल होती है।
रोकथाम के तरीके
1. शेल की वायु पारगम्यता में सुधार करें और यदि आवश्यक हो तो वेंट जोड़ें।
2. पूरी तरह से दागा गया गोला।
3. डीऑक्सीडेशन विधियों में सुधार करें।
4. गेटिंग सिस्टम में सुधार करें.
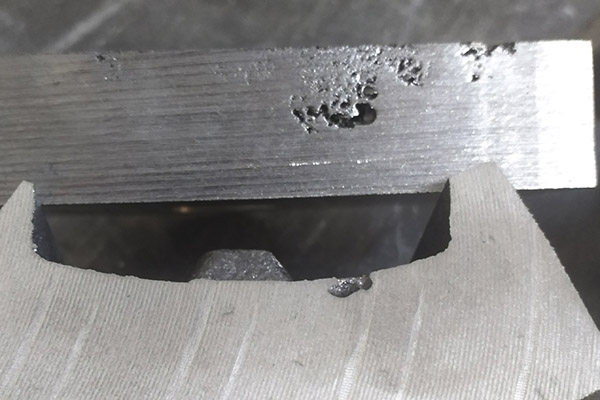
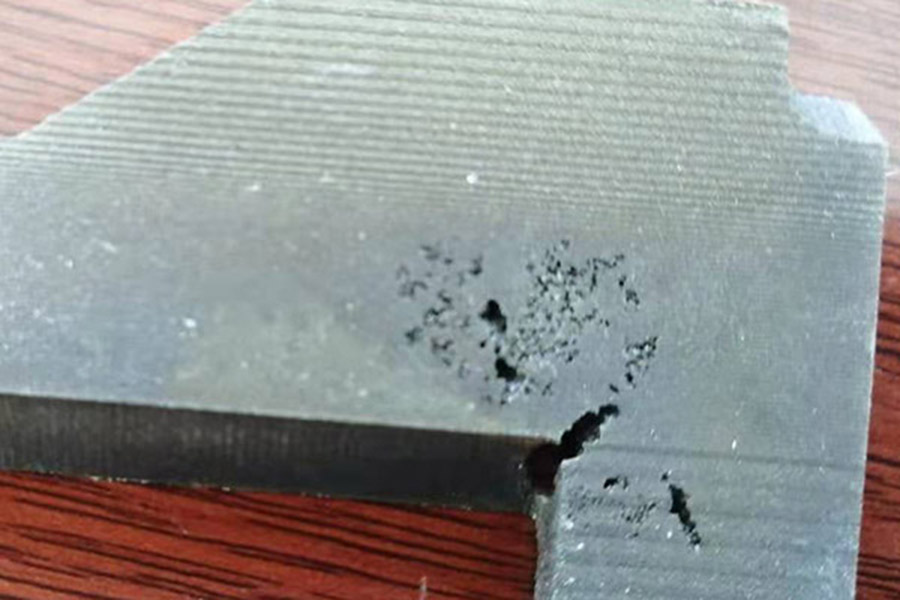
कास्टिंग पिटिंग
नाम एवं विशेषताएँ
ढलाई की सतह पर घने बिंदु जैसे गड्ढे होते हैं।
कारण
1. जब एथिल सिलिकेट का उपयोग बाइंडर के रूप में किया जाता है, तो अधूरा हाइड्रोलाइज़ेट कोटिंग प्रक्रिया में होता है, इनडोर सापेक्ष आर्द्रता बहुत कम होती है, जिससे हाइड्रोलाइज़ेट को और अधिक हाइड्रोलाइज़ नहीं किया जा सकता है, और भूनने के बाद "सफेद ठंढ" अवक्षेपित हो जाती है।
2. जब पानी के गिलास को बांधने की मशीन के रूप में उपयोग किया जाता है, तो सांचे के खोल में बचा हुआ नमक पिघली हुई धातु के साथ प्रतिक्रिया करके एक गड्ढा बनाता है।
3. पिघली हुई धातु खराब रूप से डीऑक्सीडाइज़ होती है या टैपिंग के दौरान स्लैग को साफ नहीं किया जाता है।
रोकथाम के तरीके:
1. बाइंडर के रूप में एथिल सिलिकेट का उपयोग करते समय, पानी की मात्रा में उचित रूप से वृद्धि करें और अवशिष्ट अपूर्ण हाइड्रोलाइज़ेट्स को कम करने के लिए पेंट स्टूडियो की सापेक्ष आर्द्रता में वृद्धि करें।
2. पानी के गिलास को बाइंडर के रूप में उपयोग करते समय, डीवैक्सिंग के बाद खोल को अम्लीय पानी से साफ करें।
3. सतह कोटिंग को बाइंडर के रूप में सिलिका सोल में बदलें।
4. गलाने के दौरान, डीऑक्सीडेशन और स्लैग हटाने को मजबूत करें।
चमड़े के नीचे पिनहोल कास्टिंग
नाम एवं विशेषताएँ
कास्टिंग की सतह को पॉलिश करने के बाद, छोटे काले धब्बे दिखाई देते हैं। यह घटना अधिकतर में घटित होती हैनिकल-क्रोमियम स्टेनलेस स्टीलl.
कारण:
1. धातु पिघलाने के दौरान बहुत अधिक पुनर्चक्रित सामग्री का उपयोग किया जाता है, या पुनर्चक्रित सामग्री का ठीक से उपचार नहीं किया गया है।
2. गलाने की प्रक्रिया के दौरान, पिघली हुई धातु का ऑक्सीकरण हो जाता है या पिघली हुई धातु गैस को अवशोषित कर लेती है, जिसके परिणामस्वरूप अपर्याप्त डीऑक्सीडेशन होता है।
3. शेल सामग्री की अशुद्धता सामग्री बहुत अधिक है, या बॉन्डिंग एजेंट और पिघली हुई धातु में रासायनिक प्रतिक्रिया होती है।4. गेटिंग सिस्टम की अनुचित सेटिंग।
रोकथाम के तरीके:
1. पुनर्नवीनीकरण सामग्री की मात्रा को नियंत्रित या कम करें, और पुनर्नवीनीकरण सामग्री का उपयोग रेत उड़ाने या शॉट ब्लास्टिंग के बाद किया जाना चाहिए।
2. गलाने की प्रक्रिया को सख्ती से नियंत्रित करें और डीऑक्सीडेशन को मजबूत करें।
3. फ़्यूज्ड कोरंडम, जिरकोन रेत और सिलिका सोल या एथिल सिलिकेट पेंट का उपयोग करें।
4. वेंट छेद डालने और बढ़ाने के लिए बॉटम इंजेक्शन विधि का उपयोग करने का प्रयास करें।
चिपचिपी रेत
नाम एवं विशेषताएँ
रनर के पास या ढलाई के अंदर एक चिपचिपी रेत की परत होती है, और रेत उड़ने के बाद उभरी हुई गड़गड़ाहट या गड्ढे होते हैं।
कारण
1. कोटिंग की सतह परत में उपयोग किए जाने वाले दुर्दम्य पाउडर की अशुद्धता सामग्री बहुत अधिक है, और ये अशुद्धियाँ पिघली हुई धातु के साथ प्रतिक्रिया करके कम गलनांक यूटेक्टिक बनाती हैं।
2. डालने का तापमान बहुत अधिक है, विशेष रूप से अल, टीआई और अन्य तत्वों वाले स्टील ग्रेड, जो पिघली हुई धातु और सिलिका के बीच रासायनिक प्रतिक्रिया का कारण बनता है।
3. गेटिंग सिस्टम की सेटिंग अनुचित है, और बड़ी मात्रा में पिघली हुई धातु आंतरिक धावक के माध्यम से बहती है, जिससे स्थानीय ओवरहीटिंग होती है।
रोकथाम के तरीके
1. सिलिका रेत के बजाय फ्यूज्ड स्टील जेड या जिरकोन रेत का उपयोग करें, और पानी के गिलास को बांधने की मशीन के रूप में उपयोग न करने का प्रयास करें।
2. डालने का तापमान उचित रूप से कम करें।
3. ताप संतुलन को समायोजित करने और स्थानीय अति ताप को कम करने के लिए एक आंतरिक धावक जोड़ें।
पतला करनेवाला
नाम एवं विशेषताएँ
कास्टिंग के बड़े तल पर स्थानीय सूजन, बाइंडर के रूप में पानी के गिलास का उपयोग करते समय यह घटना अधिक स्पष्ट होती है।
कारण
1. कास्टिंग संरचना अनुचित है और समतल क्षेत्र बहुत बड़ा है।
2. उच्च तापमान पर शेल की ताकत कम होती है और पिघली हुई धातु के दबाव को सहन नहीं कर पाती है।
रोकथाम के तरीके
1. संरचना में सुधार करें, विमान पर प्रक्रिया पसलियों या प्रक्रिया छेद जोड़ें।
2. शेल बनाते समय, कम अशुद्धियों और उच्च अपवर्तकता वाली शेल सामग्री का उपयोग करें, या शेल की मोटाई बढ़ाएं।
लावा
नाम एवं विशेषताएँ
कास्टिंग के अंदर या सतह पर स्लैग या अन्य मलबा है। एक्स-रे या चुंबकीय निरीक्षण द्वारा आंतरिक समावेशन का पता लगाने की आवश्यकता है।
कारण
1. स्लैग सामग्री बहुत पतली है और दोहन से पहले साफ नहीं की जाती है।
2. क्रूसिबल के टैपिंग ट्रफ पर मौजूद मलबे को टैपिंग से पहले साफ नहीं किया गया था और इसे पिघली हुई धातु में लाया गया था।
3. ढलाई करते समय, स्लैग प्रतिधारण अच्छा नहीं होता है, और स्लैग पिघली हुई धातु के साथ गुहा में प्रवेश करता है।
रोकथाम के तरीके
1. स्लैग सामग्री की चिपचिपाहट बढ़ाने और स्लैग को निकालना आसान बनाने के लिए टैप करने से पहले स्लैग सामग्री की संरचना को समायोजित करें।
2. करछुल में पिघली हुई धातु में अशुद्धियाँ लाने से बचने के लिए स्टील के सामने वाले कुंड में मौजूद मलबे को साफ करें।
3. ढलाई से पहले पिघला हुआकास्ट टीलस्लैग को तैरने में सुविधा प्रदान करने के लिए इसे उचित रूप से शांत किया जाना चाहिए।
4. स्लैग स्टॉपर या सिरेमिक फिल्टर के साथ एक चायदानी डालने वाली करछुल लें।
डीकार्बराइजेशन
नाम एवं विशेषताएँ
कास्टिंग की सतह परत की कार्बन सामग्री मैट्रिक्स की तुलना में कम है।
कारण
1. कास्टिंग के दौरान, पिघली हुई धातु और मोल्ड का तापमान अधिक होता है, और कास्टिंग की जमने की दर धीमी होती है।
2. डीकार्बराइजेशन परत की गहराई कास्टिंग के शीतलन वातावरण के वातावरण से संबंधित है। ऑक्सीकरण वातावरण की सांद्रता जितनी अधिक होगी, डीकार्बराइजेशन उतना ही अधिक गंभीर होगा।
रोकथाम के तरीके
1. शीतलन दर को तेज करने के लिए कास्टिंग तापमान और मोल्ड तापमान को उचित रूप से कम करें।
2. कृत्रिम रूप से साँचे के चारों ओर एक कम करने वाला वातावरण बनाएं, जैसे कि साँचे में बेरियम कार्बोनेट और चारकोल पाउडर मिलाना।
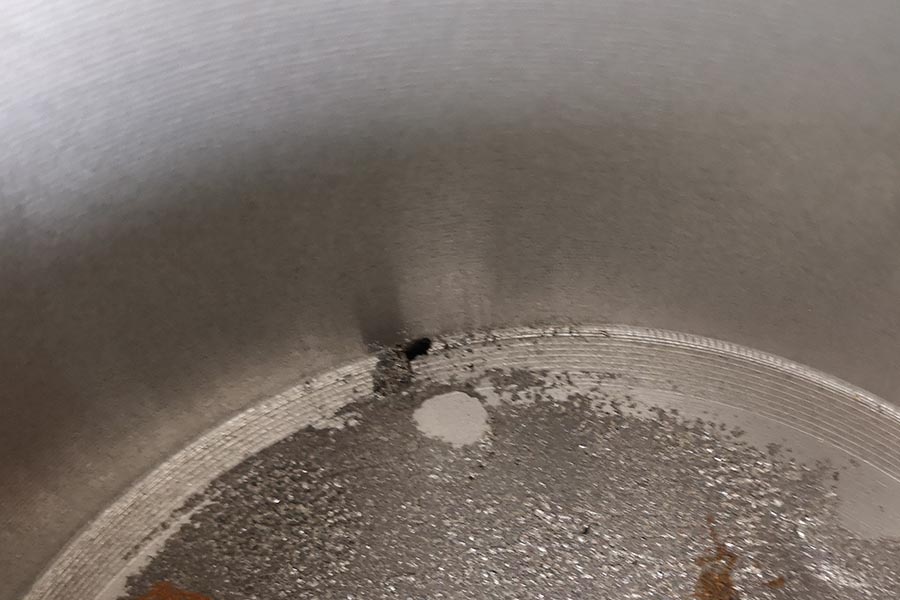
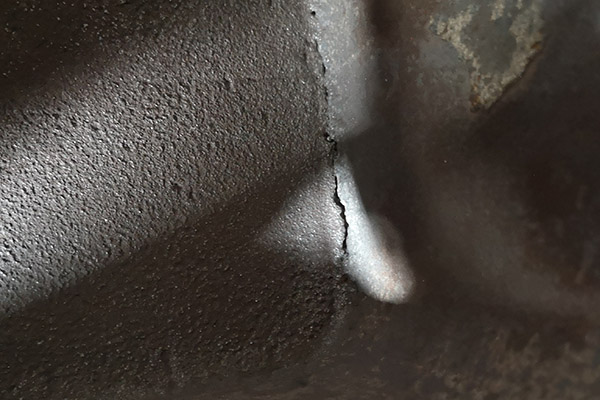
पोस्ट समय: जनवरी-22-2021