शेल मोल्ड कास्टिंगएक ऐसी प्रक्रिया है जिसमें एक थर्मोसेटिंग राल के साथ मिश्रित रेत को एक गर्म धातु पैटर्न प्लेट के संपर्क में आने की अनुमति दी जाती है, ताकि पेटेम के चारों ओर एक पतली और मजबूत खोल बन जाए। फिर शेल को पैटर्न से हटा दिया जाता है और सामना और खींचें को एक साथ हटा दिया जाता है और आवश्यक बैक-अप सामग्री के साथ एक फ्लास्क में रखा जाता है और पिघला हुआ धातु मोल्ड में डाला जाता है।
आमतौर पर, सूखी और महीन रेत (90 से 140 जीएफएन) जो पूरी तरह से मिट्टी से मुक्त होती है, शेल मोल्डिंग रेत तैयार करने के लिए उपयोग की जाती है। चुना जाने वाला अनाज का आकार कास्टिंग पर वांछित सतह खत्म पर निर्भर करता है। बहुत ठीक अनाज के आकार के लिए बड़ी मात्रा में राल की आवश्यकता होती है, जो मोल्ड को महंगा बनाता है।
शेल मोल्डिंग में प्रयुक्त सिंथेटिक रेजिन अनिवार्य रूप से थर्मोसेटिंग रेजिन होते हैं, जो गर्मी से अपरिवर्तनीय रूप से कठोर हो जाते हैं। रेजिन सबसे व्यापक रूप से इस्तेमाल किया फिनोल फॉर्मलाडेहाइड रेजिन हैं। रेत के साथ संयुक्त, उनके पास गर्मी के लिए बहुत अधिक ताकत और प्रतिरोध है। शेल मोल्डिंग में प्रयुक्त फेनोलिक रेजिन आमतौर पर दो चरण प्रकार के होते हैं, अर्थात, राल में अधिक फिनोल होता है और यह थर्मोप्लास्टिक सामग्री की तरह कार्य करता है। रेत के साथ कोटिंग के दौरान राल लगभग 14 से 16% के अनुपात में हेक्सा मेथिलीन टेट्रामाइन (हेक्सा) जैसे उत्प्रेरक के साथ जोड़ा जाता है ताकि थर्मोसेटिंग विशेषताओं को विकसित किया जा सके। इनके लिए तापमान लगभग 150 C होगा और आवश्यक समय 50 से 60 सेकंड होगा।
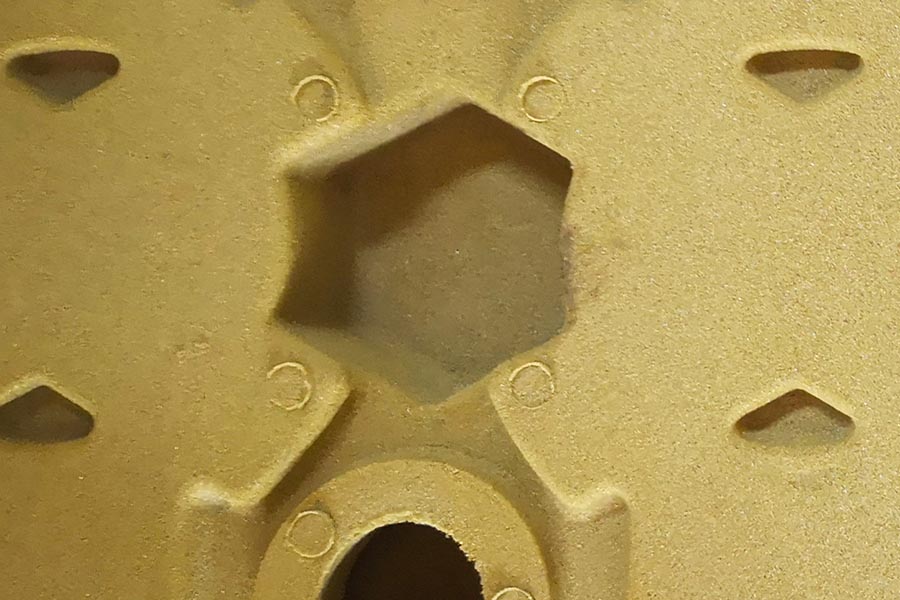
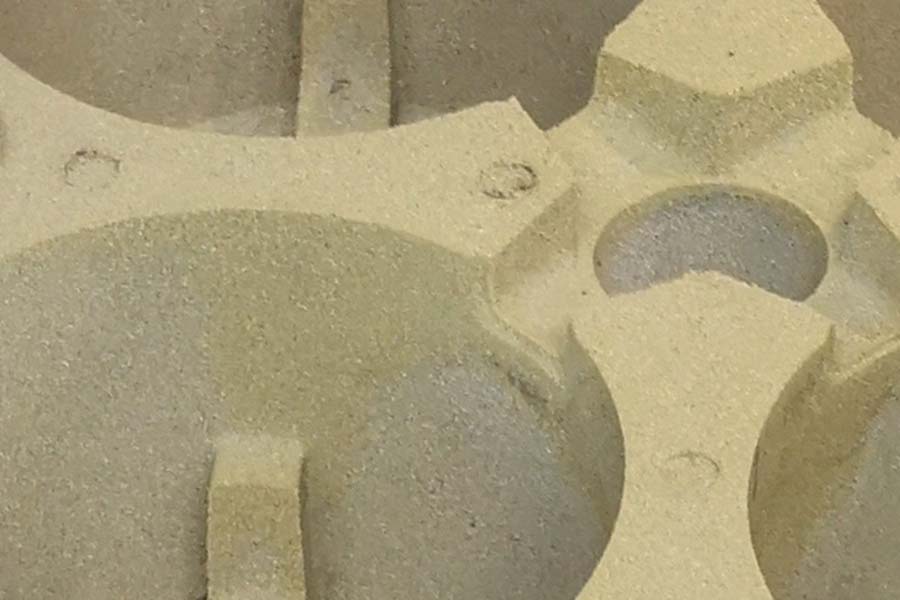
शेल मोल्ड कास्टिंग प्रक्रिया के लाभ
1। शेल-मोल्ड कास्टिंग रेत कास्टिंग की तुलना में आम तौर पर अधिक मंद हैं। स्टील कास्टिंग और +0 के लिए +0.25 मिमी की सहिष्णुता प्राप्त करना संभव है। सामान्य कामकाजी परिस्थितियों में ग्रे कास्ट आयरन कास्टिंग के लिए 35 मिमी। करीब सहन किए गए खोल के सांचे के मामले में, कोई इसे विशिष्ट अनुप्रयोगों के लिए +0.03 से +0.13 मिमी की सीमा में प्राप्त कर सकता है।
2. शेल कास्टिंग में एक चिकनी सतह प्राप्त की जा सकती है। यह मुख्य रूप से महीन आकार के अनाज द्वारा उपयोग किया जाता है। खुरदरापन की विशिष्ट सीमा 3 से 6 mircrons के क्रम की है।
3. ड्राफ्ट कोण, जो रेत कास्टिंग से कम हैं, शेल मोल्ड्स में आवश्यक हैं। ड्राफ्ट कोणों में कमी 50 से 75% तक हो सकती है, जो सामग्री की लागत और बाद में मशीनिंग की लागत को बचाता है।
4. कभी-कभी, शेल मोल्डिंग में विशेष कोर को समाप्त किया जा सकता है। चूंकि रेत में उच्च शक्ति होती है, इसलिए मोल्ड को इस तरह से डिज़ाइन किया जा सकता है कि शेल की आवश्यकता के साथ आंतरिक गुहाओं को सीधे बनाया जा सके।
5. इसके अलावा, एयर-कूल्ड सिलेंडर हेड्स के प्रकार के बहुत पतले वर्गों (0.25 मिमी तक) को शेल मोल्डिंग द्वारा आसानी से बनाया जा सकता है क्योंकि मोल्डिंग के लिए उपयोग की जाने वाली रेत की उच्च शक्ति।
6. शेल की पारगम्यता अधिक है और इसलिए कोई गैस समावेशन नहीं होता है।
7. रेत की बहुत कम मात्रा का उपयोग करने की आवश्यकता है।
8. शेल मोल्डिंग में शामिल सरल प्रसंस्करण के कारण मशीनीकरण आसानी से संभव है।
शेल मोल्ड कास्टिंग प्रक्रिया की सीमाएं
1. पेटेन्स बहुत महंगे हैं और इसलिए बड़े पैमाने पर उत्पादन में उपयोग किए जाने पर ही किफायती हैं। एक विशिष्ट अनुप्रयोग में, यदि उच्च आउटपुट लागत के कारण आवश्यक उत्पादन 15000 टुकड़ों से ऊपर है, तो रेत मोल्डिंग पर शेल मोल्डिंग किफायती हो जाता है।
2. शेल मोल्डिंग द्वारा प्राप्त कास्टिंग का आकार सीमित है। आम तौर पर, 200 किग्रा तक वजन वाले कास्टिंग किए जा सकते हैं, हालांकि कम मात्रा में, 450 किग्रा तक की कास्टिंग की जाती है।
3. अत्यधिक जटिल आकार प्राप्त नहीं किया जा सकता है।
4. शेल मोल्डिंग को संभालने के लिए अधिक परिष्कृत उपकरणों की आवश्यकता होती है जैसे कि गर्म धातु पैटर्न के लिए आवश्यक।
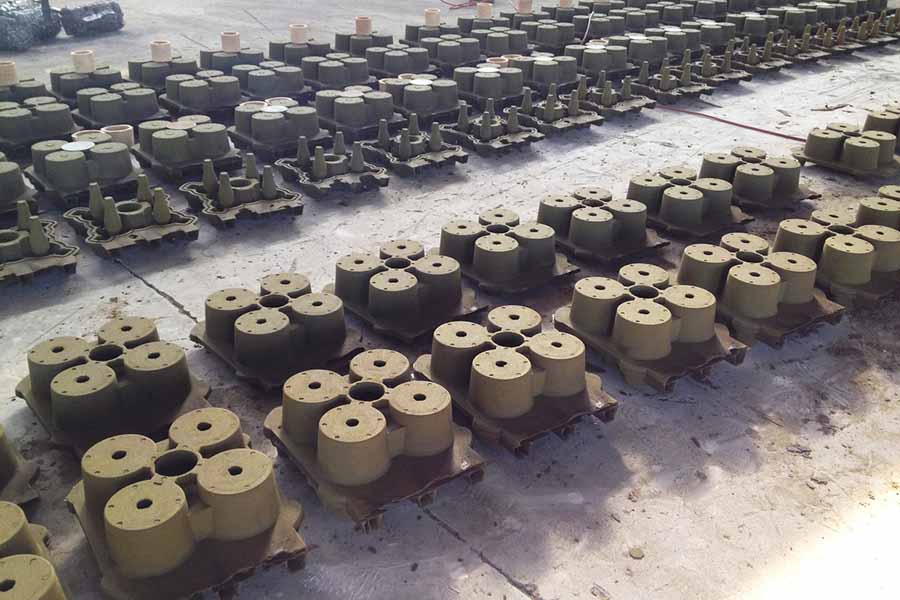
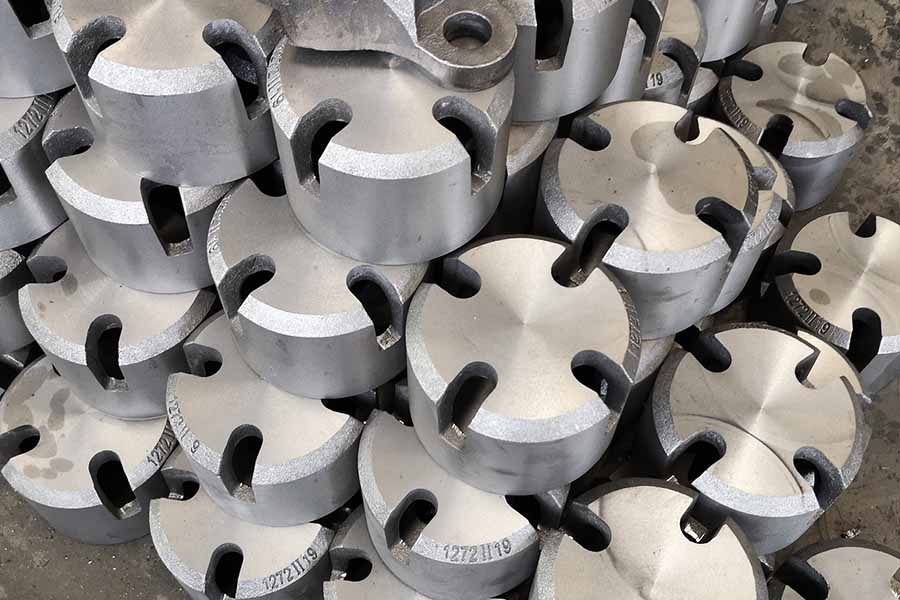
पोस्ट समय: दिसंबर-25-2020